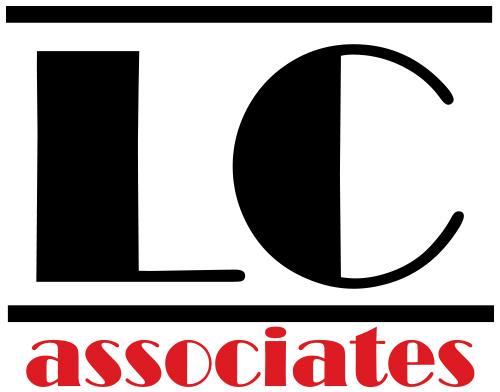
Autoclaves are machines that Hospitals use to sterilize equipment such as surgical equipment and laboratory glassware. An autoclave room is probably one of the most dangerous areas of a Hospital. Autoclaves use 250 degF Steam for about 20 minutes to sterilize items placed in its chamber.
Large Medical Steam Boiler – w/30 Gal Feedwater Reservoir
Autoclave in French basically translates to “self-locking”. Autoclaves have a chamber where a worker will place equipment that requires sterilization. The chamber is surrounded by a hollow shell that fills up with steam at a temperature of around 250 degF. The sterilization cycle lasts about 20 minutes and 250 degF steam is injected into the chamber. Once the sterilization cycle is completed, the hot steam is condensed into a liquid state.
The condensing process is necessary so that the steam can be safely removed from the autoclave. The condensed steam is typically referred to as “condensate”. Autoclaves typically use a domestic water source that has a temperature of 55 degF to condense the steam. This process, called “quenching”, can consume lots of water. The water and condensate mix is then sent down the drain. Hospital engineers can order autoclaves with a fan and radiator that uses outside air to quench the steam. However the autoclave itself is typically not located near a readily available source of outside air.
Autoclaves cannot simply use any type of steam. For example, steam generated from a central oil or gas fired boiler used for heating is not acceptable. Autoclaves require steam that is of a higher quality than steam used for heating. As a result, Hospitals typically have specialized electric boilers that flash water into steam. Interestingly, we found that these electric boilers require feedwater at a minimum 70 degF. The medical steam boilers flash the 70 degF boiler feedwater to 250 degF steam. Sterilization professionals prefer these specialized electric boilers which offer excellent response times not offered by a typical heating boiler. However the electricity supplied to the boiler is very expensive as explained below.
Autoclave kW demand without Thermal Storage. Sporadic kW demand results in low load factor, high demand charges, and high electric supply rates.
One of our Hospital Clients asked us if we can get a rebate to upgrade their autoclaves to a more energy efficient system. Our engineers installed electric interval meters on the autoclave system and observed some interesting characteristics.
From the chart shown above, one can observed a 20 kW base load for the medical steam boiler. One can also observe an additional sporadic 60 to 180 kW electric kW demand for the Autoclave array. The current operation of the Autoclave system costs the Hospital approximately $56,000 per year in electric demand charges alone….to sterilize medical equipment.
The Hospital had an array of Autoclaves located on one floor. A central medical steam boiler located two floors below supplied steam to the autoclaves. The medical steam boilers require a supply of 75 degF feedwater that it flashes to steam. Domestic water as we noted is available but only at 55 degF. Hospitals typically use domestic water as make-up to the medical steam boiler. The manufacturer designed the medical steam boiler with a 28 gallon reservoir that it kept at 75 degF in case the Autoclave called for steam. We observed that the medical steam boiler required a near-constant draw of 20 kW electric demand. This constant draw of electric power costs the Hospital about $700/month in electric demand charges.
We also noticed that the medical steam boiler was two (2) floors away from the Autoclave array. Hospital engineers had to configure the medical steam boiler to discharge 280 degF Steam as a result. The discharge temperature setting was 30 degrees more than what the autoclave required. The higher discharge temperature was necessary to account for temperature losses in the pipe distribution system. Discharging higher temperature steam requires more electricity, and is more costly than if the steam could be delivered at 250 degF.
kW Demand Simulation for supplying 140 degF feedwater to electric medical steam boilers using Thermal Storage Batteries.
One method of reducing the electrical demand charge of autoclaves is to install a steam to steam converter. This device converts house steam to medical steam. House steam refers to steam used for heating and can be of a lower quality than medical steam. This solution requires that a Hospital building has a central boiler with house steam available nearby. Even if a Hospital has house steam available, extending steam piping to autoclave may be cost prohibitive.
What we did observe is that the medical steam boilers can take feed water temperatures up to 140 degF. Flashing boiler feedwater from 140 degF to 250 degF steam requires less energy than starting at 75 degF. Configuring the medical steam boiler for a 140 degF reservoir during the day however may result in a an increased kW Demand of up to 40 kW. This condition may lower the peak demand of the medical steam boiler when flashing steam. However any demand savings will be offset by the increased kW demand necessary to maintain a higher temperature feedwater reservoir.
Phase Change Material, or PCM is a material that can be “frozen” at various temperatures. When one thinks of thermal storage, ice storage systems come to mind. However with PCM’s, manufacturers can design thermal storage batteries to “freeze” at higher temperatures. Manufacturers can make a thermal storage system to “freeze” at 140 degF for this application.
Hospitals can now charge their thermal storage batteries at night when electric rates are low and when demand charges can be avoided. For this specific Project, we designed a system where the medical steam boiler would charge charge the thermal storage battery with 250 degF Steam. In New York City, electric rates drop after 8 pm. We sized the thermal battery to store up 8 hours of 140 degF water for the Autoclaves. During the day time when electric rates are higher and demand charges apply, the thermal storage battery supplied the medical steam boilers with 140 degF feedwater. The higher temperature feedwater resulted in over a 35% drop in electric demand!
A model of the thermal storage system projected an annual cash savings of around $35,000 per year. The project itself required an incremental cost increase of approximately $150,000. The incremental cost was for the additional equipment required to utilize a thermal storage system. Fortunately for these Hospitals, their local utility company has a “Demand Management Program” (DMP). The DMP Program pays cash incentives to offset the cost of implementing thermal storage measures. Under this program, the Hospital may qualify for approximately $140,000 in cash incentives to help offset the incremental cost of the project. By using thermal storage technology, this Hospital will be able to upgrade their equipment to more energy efficient systems and save $35,000 per year.
LC Associates has secured millions of dollars for our Customers through NYSERDA and ConEdison to help offset the cost of Building Management Systems. The process to apply for the cash incentives can be found in our article “Secrets of ConEdison’s Incentive Programs Revealed | LC Associates – Energy Services“. LC Associates is also a NYISO and ConEdison demand-response provider. LC Associates is one of the only Firms that can provide an end-to-end DR and ADR incentive solution. If you would like us to secure cash incentives for your building automation project, please give us a call at 212.579.4236. You could also email us at info@cutone.org.