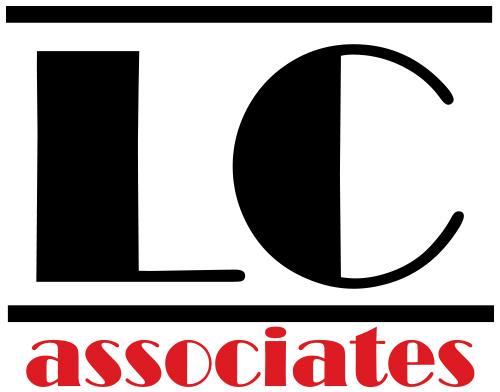
For the last 18 years we have secured cash incentives for about 26 cooling tower projects. There have been many cases however where we could have processed more of these types of projects. Unfortunately, in those cases the customer either called us after the project was completed or during implementation. Sadly, ConEdison is unable to offer incentives for any project that has already commenced.
Do not Start Your Cooling Tower Project before a Pre-Inspection!
Fortunately for those 26 Customers that called us 1 to 3 months before their cooling tower upgrade commenced. Since we had ample time to do our due diligence on their projects, we were able to maximize their cash incentives.
![]() |
When we get involved in a cooling tower project, we look at the tower as an integrated part of a larger HVAC system. The system could be a central chilled water plant or a network of distributed PTAC units for example.
About thirty percent of the cooling tower projects that we filed incentives for, were originally filed by others, or directly by the Customer. Owners’ reps typically filed their cooling tower projects as a prescriptive measure. Cash incentives for prescriptive cooling tower projects were qualifying for incentives between $5,000 and $10,000. Energy savings would come from a more energy efficient motor or control system on the cooling tower. |
LC Associates files cooling tower projects as “custom measures”. Customers that engaged LC Associates saw their cash incentives increase to between $30,000 and $70,000. The key to maximizing your cash incentive for your cooling tower project is applying for a custom incentive. Custom incentive projects require metering and verification or M&V for short.
M&V uncovers a significant amount of unforeseen conditions that prescriptive incentive programs simply are not designed to deal with. In almost all cases we found cooling towers to be operating 24x7x365 “just in case” one of the commercial tenants in a building needed air conditioning, or to maintain a minimum flow in the pipes to prevent freezing. By analyzing the cooling tower and all of the ancillary equipment it integrates with as a system our energy engineers are able to identify opportunities to save energy and maximize your ConEdison incentive.
Here are some case studies which demonstrate the important of M&V’ing your cooling tower and condenser water system so that your cash incentives are maximizes. The names of the buildings have been generalized to respect the privacy of the Owner.
![]() |
This building has a 3 cell cooling tower that was over 20 years old. The building planned on replacing the tower as it was past the end of its useful life. The Owner originally planned to use their contractor to file an application from NYSERDA. Under a prescriptive filing, the contractor expected to receive $9,000 if the new cooling tower was fitted out with VFD’s and energy efficient motors.
An account rep that worked for Johnson Controls introduced us to this owner. The Owner engaged LC Associates and we installed metering equipment on the cooling towers and the pumps. What we found was that the tower ran all 3 cells at constant |
speed 24 hours per day, every day. Each tower fan was about 20 Hp if my memory is correct. We also found that a 60 Hp primary condenser water pump operated at full speed 24 hours per day.
![]() |
We reviewed the findings with the Owner’s property manager. The property manager informed us that if there was no condenser water service the Tenants would complain. It was “safer” to leave the cooling tower running at full service in order to avoid complaints.
LC Associates’ engineers put together a proposed solution which included new towers, VFD’s, motors and a control system on both the cooling tower fans and pumps. At the time NYSERDA was offering $0.16/kWh for energy savings and a $200/kW bonus for demand response enablement. In addition to the energy savings, we implemented a demand |
response protocol that wound up increasing the cash incentive even more. We enrolled the tower into a NYISO demand response program. The Owner wound up converting that cooling tower from a depreciating asset into a revenue generator. The Owner implemented our proposed measure and was able to save about 60% of his cooling tower energy costs. The tower cells now only operate as needed to maintain temperature and we found that the primary condenser water pump was able to run at 50% speed throughout the summer. The Owner’s cash incentive went from $12,000 to just under $90,000 which offset the incremental cost of the energy efficiency improvements on the condenser water system.
![]() |
This was one of my favorite projects. We worked closely with the Hospital’s design engineers who would give us the most difficult projects to deal with. This cooling tower project took place at one of the outlying buildings that housed medical offices. The existing tower was a 2 cell forced draft cooling tower. A bright green moss engulfed the cooling tower almost entirely making it resembled a majestic living piece of art. There was one 20 Hp motor driving a common shaft powering two centrifugal fans. The original project was to be a replacement in kind. However when we looked at the data we retrieved from our metering equipment we felt |
that the Owner could upgrade the cooling tower to an energy efficient model. We suggested an energy efficient induced draft / cross flow tower. We also wanted the tower to be able to operate only one fan during part-load conditions.
Similar to the previous example, the Hospital was originally filing a prescriptive application for the cooling tower project with NYSERDA. The original application at the time was basically for a more energy efficient motor replacement on the Cooling Tower.
Working hand in hand with the Hospitals’ engineers, we thought that there was enough space to fit in a more energy efficient induced draft cooling tower. Typically, induced draft cooling towers are larger and louder than a force draft tower.
![]()
|
When the results came in, the cooling tower manufacturer was able to design a two cell induced draft cooling tower. The new tower came with a quieter fan design at an increased capacity when compared to the incumbent forced draft cooling tower. We introduced VFD’s and controls on the tower that resulted in a 50% kW demand reduction. In addition the Owner realized almost a 50% energy savings as well.
A little planning and analysis by LC Associates’ engineers wound up saving this Client a significant amount of energy savings. The resultant cash incentives were almost 5 times than originally projected. |
![]() |
Our Company is a 20 person firm which started with humble beginnings back in 2002. It’s founder has worked for one of the top engineering design firms for 10 years before founding LC Associates.
If you would like to schedule an appointment with our energy engineering Team to see if we can secure a cash incentive for your cooling tower project, please call us at 212.579.5236 or send an email to info@cutone.org |
Click here to visit ConEdison’s incentive program website