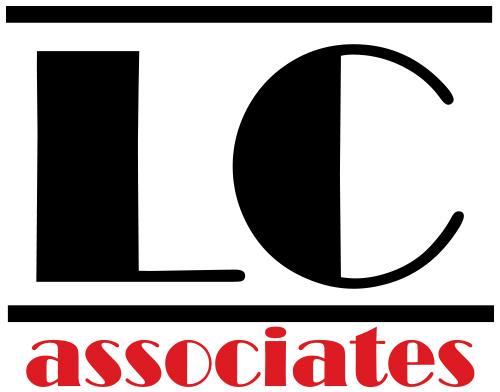
With rapid progress being made by many Countries towards favorable climate agreements, more environment advocates frequently explain why we should all be striving to make conscious choices when it comes to choosing between carbon offsetting and carbon neutral manufacturing.
New York City’s Local Law 97 (LL97) takes effect in 2024. To comply with the law, buildings owners over 25,000 square feet must reduce their greenhouse carbon gas emissions by 40% by 2030 and 80% by 2050. Starting in 2024, buildings that exceed their allocated greenhouse carbon gas benchmark will start paying $268/SF x the overage.
Most people reading this meanwhile cannot comprehend what a metric ton of CO2 or coal looks like. The image at right is an artist’s rendition of what NYC’s daily consumption of coal looks like in comparison to the UN building for example.
Likewise the next image is NYC’s daily emission of CO2 illustrated in one metric ton spheres. Each sphere has a diameter of 33 meters.
Most importantly, the fastest way to reduce this pile of coal or CO2 is to improve energy efficiency while building up renewable energy infrastructure.
“Willets Point Asphalt produces asphalt with 40% fewer carbon emissions. This project showcases our contribution to reducing green house gases”
Ken Tully, Willets Point Asphalt
Willets Point Asphalt (WPA) manufacturers asphalt for public and private roadways. Firstly, WPA is a long time customer of ours. We approached WPA to offer assistance in lowering energy costs. WPA was interested in contributing to NYC’s carbon challenge.
This asphalt plant was 15 years young with about 10 years of useful life left. Consequently, since most of our Customers are commercial office buildings, working at an asphalt plant was both exotic and challenging to us.
Our engineers contacted the plant manufacturer who recommended that we change the “drum” to a more advanced model. Since the incumbent equipment was approaching its end of useful life, this recommendation was taken seriously. We immersed ourselves in asphalt production science. Being engineers that predominantly focus on run of the mill hvac systems, we found asphalt production quite fascinating.
The operators heat up the stones to around 600 degF to remove any trace of water. Once hot and dry, the drum mixer subsequently feeds the stones into a soup of asphalt cement and RAP. Recycled Asphalt Products (RAP) consequently make asphalt a sustainable business. In short, all things asphalt can be recycled.
The mixing drum consists of a double barrel, one barrel inside the other that is constantly rotating counter to each other. The inner barrel contains a matrix of paddles that scoop up and drop the stones forming a “veil” to delay the heat escaping from the chamber.
Specifically, the conveyor systems feed virgin stones into the main drum through an aperature that doubles as an exhaust. Inside the main drum, the temperatures start at 1,400 degF at the burner end, and temper down to 250 degF at the exhaust.
A separate conveyor sytem delivers asphalt cement and Recycled Asphalt Products (RAP) into the outer drum. The asphalt cement and RAP is heated and then mixed with the hot stones which start out at 600 degF. The finished asphalt mixture is around 320 degF when it is dumped into another conveyor system. This conveyor system transfers the hot asphalt to the holding tanks.
We found that the drum itself comes new with 1/2″ thick walls. However under normal wear and tear, the walls can erode down to 1/8″. Attached to one end of the drum is a gas burner that heats up the drum’s cavity to 1,400 degF.
A blower fan sends 50,000 CFM of air through the drum. This airflow takes the heat out of the drum almost as fast fast as it enters it. Further, the exhaust temperature of the drum cannot exceed 250 degF or the dust reclamation system will catch on fire. The weakest point in this process is the exhaust temperature. If the exhaust temperature is greater than 300 degF, then the bag house will burn.
The baghouse collects dust from the mixing process and filters out dust from the 50,000 cfm airstream. The exhaust air temperature limits the speed and thermal efficiency of the process. Normal wear and tear over time can reduce the thermal efficiency in upwards of 40%.
We quickly became experts in asphalt production. The Owner could only afford to shut down the plant for about one month each year…in December. We contacted the manufacturer of the asphalt plant which helped us with some basic information and provided a foundation. However the skillset of the manufacturer, was nowhere enough to generate any energy savings projections. Fortunately we found two studies. NYSERDA funded one of the studies for the NY Dept of Transportation. A consultant in Illinois completed the 2nd study at an asphalt plant in that area.
In the end we pulled out our thermodynamics book and went to work. Engineers used old-school thermodynamic analysis to model the energy intensity of this process and all of the variables. Analysts incorporated the weather, outdoor air temperature, moisture content, insulation, air flow, production rate. The Analysts incorporated the thermal conductivity of each ingredient in the process. Field engineers took thermal images of the entire plant. The thermal images revealed the insulation and barrel had hot spots all over it. Heat that would otherwise be used by the process, was escaping to the exterior. In the end we projected a 20% energy reduction, which is translates to about 200,000 therms per year.
Before anyone asks, yes, this is a lot of gas savings. So much gas savings that it raised a red flag with the Program Administrators. You see a savings of 200,000 therms qualifies for a $1.4M cash incentive. The Program Administrator brought in experts from all over to review and analyze our projection. After all, most gas efficiency projects only saved a fraction of this amount.
The Program Administrators (PA) started calling the manufacturer and began repeating all the steps we undertook. We presented detailed analytics, narratives and math to the PA, but sadly they only agreed to a 40,000 therm savings. This ultra-conservative projection subsequently only qualified for a $280,000 incentive. The full project cost was originally $2M. Naturally a $1.4M incentive offsetting that $2M cost would certainly make the project quite attractive. Given the low incentive offer, the Customer value-engineered out much of the original project value.
When the Owner completed the project, low and behold, we observed not a 10% savings, or a 20% savings, but a 40% savings! Willets Point Asphalt reduced their process gas consumption by 300,000 therms annually! Gas savings of this magnitude would qualify for a $2.1M cash incentive to offset project costs.
Now the actual energy savings was a lot greater than projected and raised another red flag. How could the experts be off by that much savings? Was there anything else going on? It turns out that our energy projections were on the money but we left out one variable….process improvement. We wound up improving not only the energy efficiency of the plant, but also the thermal efficiency of the system. In laymens terms, more heat was going into the product than flying out the window. The Plant Operator could now manufacture the product in less time. In fact, we observed a propagation delay reduction between batches of 2 to 3 minutes. During this interval, the drum cavity is 1,400 degF and the air is still blowing at 50,000 cfm. At this magnitude of energy use, every minute contributes collectively to deep energy savings.
In any event, reducing an asphalt plants energy use by 300,000 therms per year while increasing production is an amazing fete with benefits all around.
One Standard Metric Ton of Carbon dioxide gas has a volume of 535 cubic meters. The diameter of a one metric ton sphere is 10 metres (about 33 feet). Willets Point has removed about 1,500 of these CO2 balloons from our atmostphere every year going forward.
We used EPA green house gas equivalency calcualtor to calculate the following CO2 equivalencies.
If your Company has an asphalt plant, commercial office or multifamily building over 250,000 SF that consumes energy, give us a call. We have saved NYC businesses millions of dollars and generated millions in State funding to offset energy projects for over 20 years. 212.579.4236